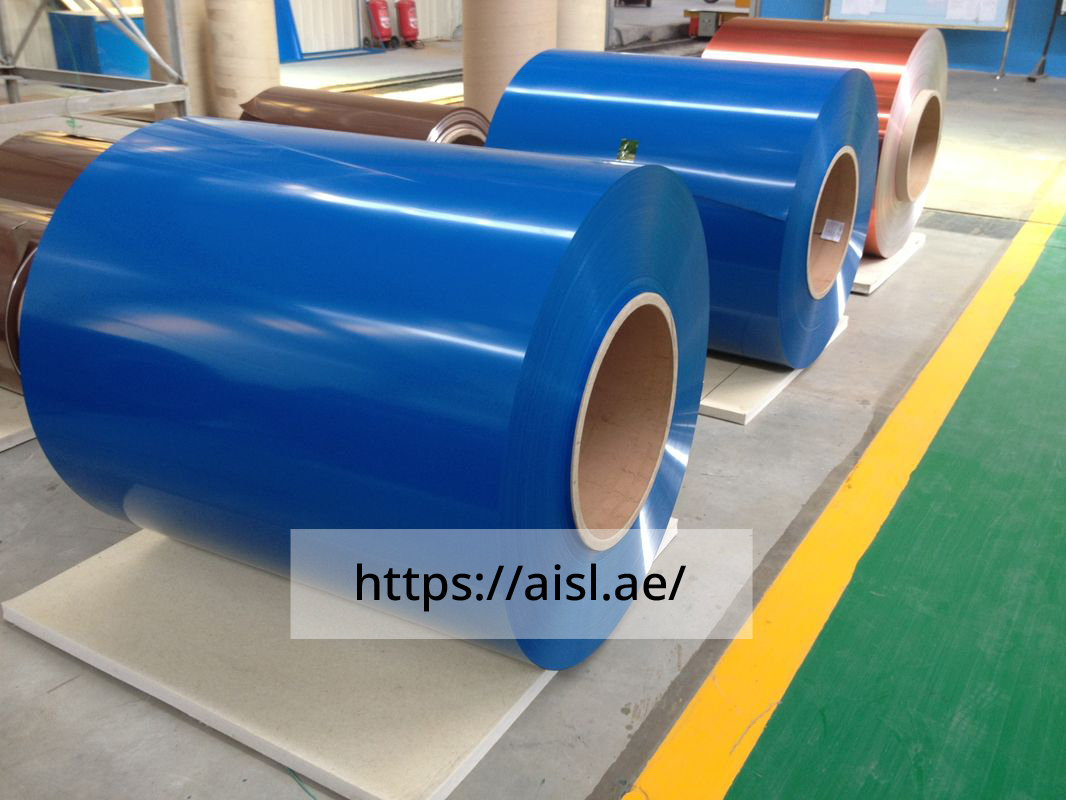
Galvanized and pre-painted steel coils (ppgi) are prepared through a process known as galvanization. This process involves coating steel with a layer of zinc to protect it from corrosion. There are two common methods for galvanizing steel coils:
1. Hot-Dip Galvanizing:
Preparation:
Steel coils or sheets are cleaned thoroughly to remove contaminants like oil, dirt, and rust. They may undergo pickling in an acid bath to remove any remaining oxides and mill scale, further preparing the surface for galvanization.
Galvanizing Bath:
The cleaned steel coils are immersed in a bath of molten zinc. The bath is typically maintained at temperatures between 815°C and 860°C (1500°F - 1580°F).
Metallurgical Bond:
The high temperature of the molten zinc allows it to react with the steel's surface, creating a metallurgical bond between the zinc and the steel. This results in a thick, durable zinc coating on the steel.
Cooling and Inspection:
After galvanization, the coated steel is carefully cooled to solidify the zinc coating. The coils are then inspected for quality to ensure the zinc coating is uniform and free from defects.
Hot-dip galvanizing is widely used for its effectiveness in providing a strong and corrosion-resistant coating.
2. Electro galvanizing (Electroplating):
Preparation:
Similar to hot-dip galvanizing, the steel coils are cleaned and prepared to remove contaminants.
Electroplating Process:
The prepared steel coils are submerged in an electrolyte solution that contains zinc ions. An electric current is passed through the solution, causing the zinc ions to be attracted to and deposited onto the surface of the steel.
Uniform Coating:
Electroplating provides a precise and uniform zinc coating on the steel. The thickness of the coating can be controlled by adjusting the parameters of the electroplating process.
Cooling and Inspection:
After electroplating, the coated steel is typically cooled and inspected for quality.
Electro galvanizing is often used when a thinner, more controlled zinc coating is required, or for specialized applications where precise coating thickness is critical.
Both hot-dip galvanizing and electro-galvanizing provide effective corrosion protection for steel coils, but the choice between them depends on factors such as the desired coating thickness, cost considerations, and specific application requirements.
How Galvanized Steel Coils Works in Rust Prevention and Longevity
Galvanized and pre-painted steel coils (ppgi) play a crucial role in rust prevention and enhancing the longevity of steel-based products and structures. Here's how they achieve this:
Galvanization Process:
Galvanized steel coils are created through a process called galvanization, where a layer of zinc is applied to the surface of the steel. This is typically done through hot-dip galvanizing, where the steel is immersed in molten zinc. Alternatively, it can be done through electroplating.
Zinc Sacrificial Protection:
Zinc is chosen because it is highly reactive to environmental factors like moisture and oxygen. When the steel is coated with zinc, it forms a protective barrier. This barrier serves as a sacrificial layer, meaning that if the steel is exposed to elements that could cause corrosion, the zinc layer corrodes instead of the steel beneath it. This effectively prevents rust from forming on the steel surface.
Corrosion Resistance:
The zinc coating provides excellent corrosion resistance, even in harsh environments such as marine or industrial settings. It acts as a physical barrier that prevents moisture and oxygen from coming into direct contact with the steel, which are two primary factors that lead to rust formation.
Longevity:
Galvanized steel products have a significantly extended lifespan compared to untreated steel. They can last for decades without succumbing to rust or corrosion. This makes galvanized steel coils an ideal choice for applications that require durability and a long life span, such as outdoor structures, pipelines, and automotive components.
Low Maintenance:
Galvanized steel requires minimal maintenance over its lifetime. Unlike untreated steel, which may need frequent painting or coatings to prevent rust, galvanized steel remains rust-free without the need for regular maintenance. This saves both time and money in the long run.
Pre painted coils (ppgi) in Dubai have a good market to captilize. PPGI protects against rust and increase longevity by providing a durable zinc coating that serves as a sacrificial layer, preventing corrosion from reaching the steel substrate. This makes galvanized steel a popular choice in various industries where corrosion resistance and longevity are essential.
Arabian Iron and Steel LLC, provides the best quality Coated steel and Aluminum to valued customers across the UAE, Dubai, Gulf, Middle East, KSA Kingdom of Saudi Arabia, Qatar, Oman, Bahrain, Kuwait, Djibouti, Yemen, Srilanka, Jordan, India, Africa, and South Asia– especially the USA, Canada, and EU. Since 2012, Ghosh Group, headquartered in Dubai UAE, has become one of the largest steel and building materials manufacturers that deliver high-quality colour-coated steel and aluminium which are used extensively in the Real Estate and Construction sector both comprehensive and small types of projects. Arabian Iron and Steel LLC, manufactures and exports a wide array of different types of Steel Products, including Prime Flat Steel Coils, which service in Transportation, Logistics, Properties, Textiles, and IT sectors.